Martin Muoto, founder and CEO of SoLa Impact, in this TPR interview elaborates on a bold and inspiring vision for rebuilding communities. Known for its transformative, impact-driven housing and real estate developments, Muoto shares news of SoLa's new Watts prefabrication plant and Model/Z home and discusses SoLa’s rapid response to devastation of the Eaton Fire—housing displaced Altadena students from Rosebud Academy and launching the Together We Rebuild benefit concert to aid uninsured and underinsured working-class families in Altadena. With unshakable optimism, he also lays out his ambitious plan to make Pacific Palisades a cutting-edge, reimagined community, turning disaster into an unprecedented opportunity for renewal. Muoto most importantly addresses: resilience, economic mobility, and the urgent need for reinvestment in California’s hardest-hit neighborhoods.
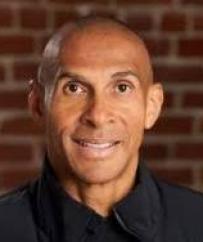
Martin Muoto
“There’s no reason why rebuilding should take five to seven years. The technology exists, the capital exists, but what slows everything down is bureaucracy. If we don’t challenge that, we’ll end up with a drawn-out process that benefits no one.”
Martin, it's almost been two years since TPR last interviewed you. Update readers on SoLa Impact’s housing developments and initiatives begun since.
Over the last three years, we completed several hundred ground-up units. We have about 32 projects with over 3,000 units and we've completed about a third of those. All of these projects are affordable and workforce housing in the broader Southern California area, exclusively in low-income communities, which has been our focus since the company’s inception. We now have a few projects in San Diego, but the majority are in LA — with a number in South LA and the Crenshaw District —but also a few in East LA and the Valley. Of the 32 projects, a third are complete, a third are in active construction, and a third are in the entitlement process.
Almost every month, one of our buildings gets to certificate of occupancy (CoO). Like a marathon, the last mile is the hardest. We are actively working with LADWP, the City, the County, and various building departments to accelerate things. Yet it continues to be painfully slow and inefficient—but we remain committed and hopeful. While SoLa has built more affordable housing units than any other private developer—and has built units better, faster, and more cost-effectively—the process is still woefully inadequate and the industry is still not coming close to meeting the demand for affordable or workforce housing in California.
Elaborate on SoLa’s privately funded, for-profit, affordable housing model that results in new housing units built for under $300k ‘all in’ without government subsidies.
Our investors include several family offices and institutional investors, such as PayPal and the California Teachers Retirement System, insurance companies like Equitable and Standard Life, and multiple banks, including PNC, Pacific Premier Bank, and Ally Bank. Most of our capital comes from family offices, often led by entrepreneurs who have built very successful businesses. We do not use government subsidies such as Low-Income Housing Tax Credits (LIHTC) to build. These take too long, are very bureaucratic, and are highly inefficient. As you and others have reported over the years, it leads to building costs of $750K to $1 million per unit.
Three years ago, we were building at around $250,000 per unit. The entrenched players said it couldn’t be done. They said it simply wasn’t true, that we were lying. So we had it audited by a third party, and at the time, it was $253,000—so yes, I was “lying” by 1%. Today, on average, we are still under $300,000 “all in” per unit.
But our goal, in no uncertain terms, is this: We want to scale to 10,000 units per year at $200,000 per door, all in. When I say “all in,” I mean everything— land costs, hard and soft construction costs, financing costs, City fees, permitting fees, design and architectural costs, engineers and consultants—everything. We believe we can achieve that 10,000-unit goal and the $200,000 per door with our modular technology if we get some cooperation from the government, the City, and—at least a little—from the bureaucrats.
How has SoLa Impact been able to scale? Elaborate on your partnerships, for example, with Zenerate.
Zenerate is one of the great software development partners we work with, but let me take another step back.
Over the last 5 years and in over 30 projects, I’ve learned a lot about scaling an affordable housing development platform—and I have probably made every mistake in the book. I used to have more hair, but I pulled it all out dealing with the inefficiency of today’s entitlement and construction process and LA’s bureaucracy.
I often say that a third of the issues were our own mistakes, a third were with general contractors, and a third were the city and county red-tape. It’s extremely difficult to scale affordable and workforce housing using the same tools and techniques as every other builder. I’m not just talking about LIHTC—I mean the fundamental inefficiencies and conflicts in every step of the design, construction and financing process.
You have architects who want to design in completely different ways but do not want to be overly prescriptive to avoid liability. Structural engineers and consultants trying to engineer with conflicting agendas. Do not get me started with the GCs—general contractors see ambiguity and conflict as a great opportunity for “change orders” which are their largest profit center.
The entire ecosystem and process is dramatically inefficient, uncoordinated, and misaligned. The only logical solution—specifically for affordable and workforce housing— is radical “simplification, standardization, and streamlining.” This led us, about three years ago, to make a strategic decision to shift towards modular construction.
We visited probably every modular factory in the western United States and Mexico and quickly realized they all suffer from the same fundamental problem. Today, they’re bidding on a SoLa project because we represent a very large customer. Tomorrow, they’re bidding on a senior housing project in Santa Fe. The next week, they are trying to land a Hyatt Regency extended-stay hotel. The following week, it’s a school in Montecito. These projects have nothing in common. Everything is custom.
This is my analogy: One day, they’re building an Audi sedan. The next day, they’re building an oversized SUV. The day after, it’s a convertible sports car. No automotive plant is set up this way. We would never build cars this way. So why are we building housing this way? Every time today’s modular vendors win a new customer, they have to reconfigure their entire production line and reinvent their entire supply chain—new faucets, different fixtures, new cabinet dimensions, different layouts. They have to reconfigure their assembly process and inventory because one client wants 8.5-foot ceilings and the next wants 9-foot ceilings. Each new client wants different tile or floor coverings. Each project has different floor layouts than the next. There really are no process learnings or improvements from one project to the next, and certainly no true economies of scale.
We don’t make clothing this way. You and I wear clothes off the rack. No one builds custom-designed cars from scratch because it would take four years and cost $2 million to deliver one car. But for some reason, we build housing this way. So we chose to flop that model on its head.
We started with one universal chassis: a 420-square-foot one-bedroom unit that meets all LA building codes, all the federal HUD standards, the Section 8 requirements, and ADA Chapter 11B accessibility rules. This really is the “superset” for affordable housing, and meets the building codes of 95% of California’s municipalities. This becomes the Lego block for every building we construct. While our buildings can look highly customized—because you can build quite complicated structures with Lego blocks—the fundamental “two-by-eight” Lego piece never changes.
SoLa has successfully raised outside, priavte capital and invested in a volumetric modular facility that has been operating in Watts for the last year. Share more about this factory’s product, use of AI technology, and production capacity.
We looked all across Southern California to try to locate a facility. We were looking as far as Redlands and the Inland Empire. Every suitable building was being bid up by distribution and logistics companies. We were about to sign a lease in Bakersfield, which is almost three hours away. Perhaps through divine intervention, we found a 160,000-square-foot facility in our backyard of Watts. I was simply overjoyed as bringing hundreds of well-paying jobs to a historically overlooked community like Watts aligned deeply with what SoLa has always strived to do.
We hired an executive team—mostly from SpaceX, Google, and Toyota—essentially the top aerospace and automotive companies. We unleashed them on designing and redesigning our first Model/Z, inspired by Henry Ford’s saying, "You can have it in any color, provided it's black," and the same philosophy: "You can have it in any variation, provided it's the Model/Z"—our 420 square foot two-by-eight Lego block.
Our vision is to use this same Lego block for different building configurations but to dramatically increase the scale and reduce complexity—thereby controlling the cost and quality of affordable housing and workforce housing. Again, it doesn't work for the luxury housing market or hotels. But that is really only part one of the strategy for Model/Z—really just the first concentric circle of our vision.
We are in the second largest city in the US, with the largest homelessness problem in the country. California also has the largest shortfall of affordable housing nationally. Since the LA fires, there are now yet another 15,000 families without homes. This only worsens the housing needs of the region. So this is a massive problem.
In its first year, the Model/Z factory was able to scale production to two units per shift, which is a testament to the outstanding operating team and better than 90% of the modular vendors in the United States, and we've met with most of them. We will be able to announce our first non-SoLa customer in a couple of weeks and are in discussions with about a dozen developers, churches, university systems, and government agencies.
The second concentric circle is our significant investments in software and AI—Zenerate is one of the great software development partners we work with— that allows us to take any lot across LA and, within minutes, tell you whether it's amenable to modular construction. Not all lots are. The plot has to be flat enough; it has to have a wide enough road; it cannot have overhead power lines to obstruct a crane, and so on. We can also tell you the optimal configuration given different constraints and density incentives leveraging AI’s machine learning capabilities informed by our extensive data sets and hard-earned, real-world experience. We can also give you a massing and the economic feasibility without the involvement of an architect or consultant. So there’s the identification of lots, the economic feasibility, and massing—done entirely in software.
Eventually, we want the ability to use that software to do everything a plan checker does. A plan checker is essentially an expert system of rules that determines, “Do you have the right setbacks and FAR? Do you have the correct low-impact development calculations? Is the electronic transformer sized appropriately and in the right place? Do you have your load calculations correct?” It's pretty much all math and rules. That's the second concentric circle of Model/Z—to use AI and technology to dramatically streamline, simplify, and scale the design and entitlement process, again, given the fundamental building blocks of the Model/Z “lego” pieces. This makes things radically faster, cheaper, and more predictable.
We need the City to buy in and we're spending time with the masterminds and thought leaders who influence policy—most of whom read your Planning Report. Our factory in Watts, at capacity, can produce 5,000-7,000 units a year. Our goal is 10,000 so we plan to add a second factory. We are currently building the second concentric circle, which is the AI software to dramatically expedite and simplify the permitting, entitlement, and design process.
Our third concentric circle is as follows: you drive to Watts, South LA, East LA, almost any low-income urban community in California and you realize that a large percentage of the land is underutilized. It’s large church parking lots that are only used on Sundays. It’s vacant land and abandoned buildings. Its single-story retail that is barely open during the day. The owners are families, mom-n-pop business owners, and institutions – many of whom have owned this land for decades. Our hope is to help these families, institutions, and business owners create and retain intergenerational wealth by unlocking the “higher and better” use of their land while persevering their ownership.
SoLa’s business model has historically required us to buy land from local owners in order to develop affordable housing on that land. It works for those that want to sell. But we don't want to have that as our only model. There will be many that want to sell, but what I also want is to be able to go to those landowners and say, “You don’t need to sell. You own a 10,000 square foot lot. It's being used to sell used tires. You're getting $3,000 a month. Our software said this is perfect for modular. Our software has identified that you can build 82 or 102 affordable or workforce units on your lot using LA’s ED1 incentives. Would you consider doing that?” They hopefully go, “Well, I would consider it. What does that mean for me?” Then we explain, “You can go from earning $3,000 a month to $13,000 a month.” I think most of them respond, “That's great. I'm super interested!”
Our software – with the City’s cooperation – will allow us to submit plans on their behalf, within weeks and for pennies on the dollar. Our proposal to the various building departments is, “Look, this family is looking at building 102 affordable housing units.” We submit these software-validated plans on behalf of these families. Under the best-case scenario, the city ratifies the software so that within days, perhaps minutes, the software-enabled process certifies that it meets all the building codes, has the right structural calcs, meets all the compliance requirements – again, much like plan checkers and inspectors – after all it's a giant expert system that improves over time.
Some municipalities will adopt this because they are desperate for affordable housing and want to genuinely solve the problem by leveraging technology. Others may not but will simply get bored of looking at our software-configured plans because they're all picture-perfect, always correct, and we're not trying to hide any inconsistencies. This allows us to go back to current landowners very quickly and for very little cost to say “Guess what? You've been approved for 102 units. When do you want to start to build” At some point, we will help them construct, or finance, or lease, or manage those thousands of units. This really is the ONLY way to truly solve homelessness and bridge the affordable housing gap at scale. We know this having tried every other way.
I'm an entrepreneur. I am, for better or worse, a disrupter. My team calls me an “urban cowboy” and I get all the good and the bad associated with that. You can see how disruptive this model would be to the traditional affordable housing industrial complex. But it builds real intergenerational wealth in communities in desperate need of means of doing that. It does so without gentrification or displacement. And while it doesn't put SoLa out of business…if it did because this new model was so effective, I'd be okay with that outcome.
To rebuild, new housing must meet local building and safety standards. To expedite approval processes, what, from your experience, can be improved, not only in LA but in California? What can be improved regarding utilities, not only in LA but in California?
We recently had the LA fires, and I’d been on the phone with the building departments, the city council, and the Mayor's office. To their credit, they responded, and I applaud them in giving impacted communities certainty, clarity, and speed.
I lost every material possession I owned to the fires. My home that I personally built with my wife over countless hours and two grueling years. All my socks, all my underwear, my African art, my high school yearbooks…the wine had saved for a special occasion— gone, gone, and gone. I was at the job site of my home every day at 7 am for two years because I'm a cost-conscious control freak. I knew every square inch of that home, every fixture, every tile selection, and I lost it all. It's gone, and it took me about 72 hours to remember: Thirty years ago, I came to the United States with nothing, and I will leave the earth with nothing. In between, you accumulate a lot of “stuff” right? Yes, it's stuff that I've worked very hard for. I don’t want to minimize anyone else’s grief or response to the crisis and it breaks my heart that so many are in pain. Many are uninsured and underinsured and that is a real crisis. You never know how you react until you've actually been through it, but for me, the experience gave me even more clarity as to what is really important.
The LA fires greatly simplified SoLa’s mission and purpose: to house the most vulnerable members of society and create wealth for communities that have been historically marginalized using innovation, entrepreneurship, and the free markets. That’s what I was put on earth to do. It’s given me an incredible sense of urgency.
60,000 people were experiencing homelessness a month ago, and now it’s over 75,000. The 60,000 who were homeless before the fires are still homeless today. Yet, they will now have to “compete” for City resources, attention, and priority with the 15,000 well-resourced families looking to rebuild their homes.
Mayor Karen Bass, with the most recent Executive Order, enacted perhaps the most comprehensive set of reforms in housing of the last 30 years. Now, there is suspension of normal procedures, and the governor temporarily suspended CEQA and Coastal Commission. These responses promise to dramatically reduce the bureaucracy and red tape that accompanies building in Los Angeles.
There was also mention of encouraging modular construction, which we believe is inevitable. The Mayor’s executive order required accelerating certificates of occupancy for affordable housing. I hope these actions trickle downstream to actually reform how affordable housing is entitled and built. I think Mayor Bass’ heart is committed, so let's use this opportunity to reinvent that process. You should never never let a crisis go to waste. When I speak to the various building department leaders and even LADWP, they all agree it’s what we should do, but we need the conviction and courage to actually get it down.
You referenced the Palisades, but Altadena is another community that was devastated. Can you share what, if anything you’re doing for Altadena?
We're doing two things immediately. First, the Beehive is providing a temporary school for 120 students from Rosebud Academy from Altadena, grades K through 8.
They arrived here today (Monday). They and their parents were quite apprehensive about being “bussed to South Central LA.” It’s quite ironic. Yet when they saw our Beehive campus and the state-of-the-art Tech Center…let's just say there were a lot of tears of joy, and they weren’t just mine. It’s also providing comfort for the parents, giving them a safe place and a respite from the chaos out there. This is our immediate response with our resources and staff helping out. The teachers are here, and the principal is here as well.
The second thing we’re doing is working on organizing a concert at The Beehive on February 22 called Together We Rebuild. We’re hoping to bring in some of the coolest acts in LA to help celebrate and raise money for the rebuilding of Altadena. The net proceeds will specifically go to working-class families in Altadena who are uninsured or underinsured, so they don’t have to sell their homes. There are vultures offering bargain prices for their land, and we want to provide legal resources, financial advice, and some capital to help people hold on to their homes. Whatever we raise will go directly to working-class families from Altadena. As you may be aware, Altadena has historically had a very high rate of African American homeownership, and we want to help preserve that.
Martin, without being too personal, will you be rebuilding your home?
I want to be the first house rebuilt in the Palisades. It's a unique community of industrious, resourceful, and hardworking families. I think I’ve shared a lot but suffice it to say that if ever in a crisis, there is hope and there are good things that come out of the ashes. I think this will make us stronger and I hope it shows the world how resilient Angelenos are.
- Log in to post comments