Appointed as Chief Executive Officer of the Port of Long Beach in June, Jon Slangerup joins POLB with 34 years of corporate leadership experience—including expertise in aviation, logistics, and clean technology. In agreeing to head a seaport that moves $180 billion worth of trade annually, Slangerup faces logistical and technological hurdles that the port must overcome. In this interview with MIR, he discusses current infrastructure challenges and improvements at the Port of Long Beach, efforts to green operations, and POLB’s relationship with the Port of Los Angeles. He also remarks on POLB’s economic health and awareness of growing global seaport competition.
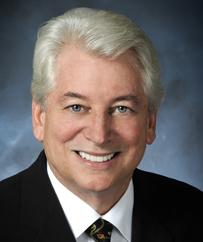
Jon Slangerup
“We’ve invested not just in cleaner trucks, but also in cleaner locomotives, along with technologies installed on our docks that allow ships to plug into shore electric power, eliminate diesel operations of cranes, and so forth.” -Jon Slangerup
What, Jon, enticed you to accept the position of Chief Executive of the Port of Long Beach?
Jon Slangerup: Obviously, the Port of Long Beach is an extraordinarily important operation—a gateway to trade in the US.
I wasn’t a port-experienced executive, so I was quite surprised to get the call. It took me a bit of time to get my head around what they were looking for. As they began talking about the opportunity, it became apparent to me that my large-scale logistics background was certainly appropriate for addressing logistics, efficiencies, and challenges within the entire system model, as well as the major capital project that was underway and needed some guidance. I had experience with all of that at a large scale in my prior job. There was also tremendous interest in expanding the sustainability and environmental stewardship of the port, which was a big deal. Both of those things—the fact that I had experience in sustainable technology, as well as a background in logistics—attracted me.
Personally, I’ve always been attracted to larger–scale activities because of the large impact you can make with a larger footprint. The Port of Long Beach has an incredible reputation around the world, and it’s a very prideful thing for me to accept this job.
Leadership of POLB requires addressing a number of challenges, including: operational goods movement logistics, attendant environmental sustainability impacts, and the need for capital investments. Share how POLB will be addressing these.
Certainly. This is a time when there is a rapid transition occurring in the industry. Massive ships are being built and deployed into service. This has driven a lot of changes—not just operationally, but also from a relationship standpoint among the carriers. The steamship lines have banded together in alliances, which is now the common approach to doing business. Big ships facilitate and force that. This is changing the entire makeup of how we deal with the marketplace and also with operations.
We’re handling now 14,000 TEU vessels on a regular basis. Next year, we’ll start to see even larger ships come in. It’s a challenge, from an operational standpoint, to see a massive amount of volume increases in a short period of time. It puts enormous pressure on traditional operations—not just dockside, but also on the rail side and especially on the trucking side. Getting that volume in and out of the ports in a short period of time has always been a challenge, but when you double ship size, it makes it even tougher.
We’re reacting to that on an accelerated basis. The investment that we’re making is tied to that. The impact is broad, because we need to look at the system all the way from the origin to the destination. The Beneficial Cargo Owners are also pressurized to receive their freight. Any delays in the system impact their ability to get their product to market. Throw on top of that the steamship lines started some time ago to get out of the chassis business. Suddenly chassis have become a major issue in managing these assets on a effective basis on the docks.
A lot of moving parts, a lot of complications, a lot of conflict resolution, and a lot of investment being made make for a pretty interesting mix.
Elaborate, to afford our readers better insight into POLB’s challenges, on the nature of the chassis issue you mention.
A chassis is a trailer on which these large containers are mounted. Each chassis is owned by one of several individual companies, so the chassis have to find their way back to the owner. The trucker moves the container to its destination, then often comes back empty to return the chassis, making for very inefficient operations.
The industry is moving toward a gray chassis fleet, meaning all will be interchangeable. Chassis owners will simply have a number of chassis, receiving income from a per diem rental on an individual unit basis.
Today, those companies discreetly own chassis, so they are trying to manage their inventory and make sure chassis are available to the various terminal operators and to trucks. It’s a very complex thing.
We’re in the middle of a massive change where the three principal groups that own the majority of the chassis are cooperating on an asset management system. They very recently received permission from the Department of Justice to have dialogue about organizing a management system that allows them to compete, but also allows them to manage this chassis fleet on an integrated, interchangable basis. For us locally, it’s going to be step one of a big improvement in that part of the congestion problem.
We’ve been working diligently the past year with all of the stakeholders to come up with a chassis management solution. We’re about ready to launch that, and by the end of this year we hope to have it in place.
Please elaborate on POLB’S Technology Advancement Program—what technologies are being invested in and why?
We’ve been investing for some time in all forms of technology, particularly in sustainable technology that allows us to hit our emissions targets. California leads the world in strict emissions standards, for air emissions as well as water quality.
CARB dictates specific standards to be met on air emissions. We call the achievement of those objectives “attainment.” A big attainment goal was set for 2014, with a big step up in 2023, and another in 2028.
Through our investment in technologies, we have achieved the 2014 numbers—extraordinary improvements in air and water quality. We’ve invested not just in cleaner trucks, but also in cleaner locomotives, along with technologies installed on our docks that allow ships to plug into shore electric power, eliminate diesel operations of cranes, and so forth.
I’ll give you three examples. First, we are currently building one of the largest terminal operations in the world, and it happens to be the world’s first all-electric operation. Everything there—from overhead cranes to automated container movers, and even to vessels that plug into our electrical systems—is all-electric. This terminal is so large that, by itself, it will be the fourth-largest port operation in the United States. It’s a very significant project, with $1.3 billion investment in the most advanced, automated technologies known in the industry.
At the same time, a few years ago we invested in the Green Truck Program. That resulted in providing incentives to the trucking industry to spend $1 billion on replacing its entire fleet, from old trucks to new, cleaner-diesel truck models. They complied and it dramatically changed air emissions within the port, dropping pollutants by 86 percent. We initiated that change with our sister port, the Port of LA. It has gone a long ways toward achieving our air emissions goals.
The third area is in our own locomotive and rail operations. We have dramatically increased the amount of on-dock rail. In the past, when ships were offloaded, they put containers on the ground, stacked them, put them on trucks, and moved them out. On an increasing basis, containers now move right from the ship onto a rail car, then are moved off of the terminal property and loaded onto long trains that move directly by rail into the interior of the US. Over the last five to six years, we’ve gone from about 15 percent on-dock rail capacity to about 24 percent today. We’re moving to about 35 percent over the next few years—a $1 billion investment we’re making in rail. We’ve also seen our Port’s short-line locomotives transition to Tier 3 clean diesel engines—a big capital investment.
We are extremely focused on not just efficiency improvements that drive the velocity of our terminal operations, but also on investing in equipment that dramatically lowers the carbon footprint and emissions of these operations. It’s a very serious effort. Fundamentally, economic sustainability and environmental sustainability are two faces of the same coin. I’ve always believed that, and its one of the most exciting things about this job.
Moving goods through POLB with velocity and at a reasonable price to their destination is obviously a priority. Share how the port is addressing this challenge.
Today, the Port of Long Beach is the most productive port operation in the United States, with LA very close behind. The two ports together are very effective at moving cargo from the ship to the dock.
Like I said, ships are so large now, and the volume of container traffic so significant, that it has changed the way trucking operations work. When you’re improving the on-dock rail part that doesn’t touch a truck, still 75 percent of all that movement is truck-based. A large influx of containers at a given time certainly drives the waiting time for the truck operations. They have to line up. Instead of being in and out within 30 minutes, sometimes it’s an hour or an hour and a half.
A few years ago, our terminal operators introduced a system called “PierPass”—the first time we saw expanded traditional hours-of-operation of our terminals. We went from one eight-hour shift to an almost two-shift operation, which relieved some of the pressure. Of course, the labor cost of being open longer hours had to be absorbed, so PierPass created a fee structure to offset these costs.
Today, we need more flexibility on truck access to containers and yards. We’re looking at systems that will create the next generation of PierPass, effectively creating a demand-based information system where freight could be made available at a certain time and truckers would show up at that appointed time to be assured a shorter turn time.
The crisis that we’ve been dealing with is that truckers, at this moment in time given the volumes, are not achieving the turn times they require to make multiple trips. The more turns they can make, the more money they can make. When you’re in line for a long time and you can only make one turn during your shift or during your allowed time, then you can’t make the kind of money necessary that makes it worthwhile. We’ve got to solve this with better scheduling and better access to freight on a much more flexible basis during the day.
Talk a little bit about the governance and goals of transport in and out of the port, and how you relate to that as head of POLB.
We’re a landlord port, which means that we don’t actually operate our terminals. We’ve got partners or customers that lease these facilities from us long-term, and we work with each of them to provide the most up-to-date facilities.
Nevertheless, even though we are not directly involved in the operation, we have a responsibility to facilitate changes as necessary within the overall operations. We bring stakeholders together and come up with specific solutions. PierPass was an example, and its next version will be another, along with the chassis situation.
Our job as a facilitator is to identify the problems, bring people together, overcome differences of opinion or self-interest issues, and come up with a common solution that works for everybody.
In order of priority for us, on-dock rail is a proven way to alleviate congestion. We’re making that investment and continuing to increase our capacity there. Second is the chassis management program. Third is applying advanced technologies and information management to the entire supply chain. This will allow everyone that touches freight to have visibility as to where a container is located and its status—speeding the process from ship to warehouse throughout all of the various logistical steps.
In the future, we’re looking at improving emissions profiles of ships, trains, and trucks, and moving to hybrid technologies. Now, we’re testing emissions management systems for ships that can’t plug into our electrical systems (about half are not equipped to do that.) An alternative technology we are testing will allow all other ships in our ports to have a near-zero emission profile. We’re also testing hybrid-electric trucks that we believe are the next generation of tractors. In some cases, those will be electric tractors. Emission profiles will drop steadily over the next five to ten years, and we’re confident that we’ll hit our emission attainment goals for 2023.
Can you quickly address the rail connections from both ports and what they portend for the future?
Systems or consolidation points like the proposed SCIG facility are commonly used today. Union Pacific has a facility that works very effectively—a joint facility run by both ports for UP. BNSF is working on the same thing with SCIG. They’re currently involved in addressing some environmental concerns and related lawsuits, but we’re hopeful those will be resolved. We’re very supportive of off-dock operations, providing a place to take mixed container freight, break it down, reconsolidate it, and send it out on its way. The more freight you can take off the dock, or off the terminal property, the less congestion you have. The key is to move as much of the volume near dock or off dock as quickly as possible, to provide as much real estate for the trucks and the terminal operations to move freight around. That’s the fundamental goal of these systems and facilities in which we have invested.
In the spring, we interviewed then-Mayor Bob Foster of Long Beach about a City of LA commission’s proposal to combine the two ports. I think it is fair to say Mayor Foster thought that was an idea that had no business reason. Is that discussion still alive?
The discussion is pretty well put to bed. I think those on either side, particularly the two new mayors of both cities, feel that it’s a non-starter. Gene Seroka, the executive director of the Port of LA, and I think that competition between our two sister ports is extremely important. We call it “co-opetition.” Quite frankly, we cooperate on many fronts, relative to making sure the economy, jobs creation, and growth of the ports in the San Pedro Bay area continue to improve. We do that on environmental and technology-development issues common to the ports—from community outreach, to environmental sustainability, to compliance.
Our two ports have a history of working together, but at the same time we’re fierce competitors. This attracts business to Southern California. You can see from the results. We are the dominant player here in the United States as a complex, and individually we are very large operations—each carrying about 20 percent of the trade in the United States. It’s a very good system. Competition is healthy. We think that, if we combined, there would not be an improvement in operations—in fact, there would be a risk of being less competitive.
Let’s close by asking you to assess your competition, especially from the widening of the Panama Canal now almost complete, but also from Prince Rupert in British Columbia.
I think Prince Rupert is doing a great job in building their port operations, rail connections, and so forth. There is a certain amount of volume that is going to go their way. We haven’t seen it from a market share loss perspective at all, but I think that as the market expands, they will take their share of the growth. They’ve got very good operations and are well managed. But they’re small and will remain small.
Trade goes where the market demands are—and the Southern California gateway is the big draw for the US market. We think it’s very positive to see Tacoma, Prince Rupert, and some Mexican ports coming on strong. That’s not a bad thing.
We see opportunity on a net basis, more than a concern about loss of business to the new Panama Canal that may open in 2015 or 2016. Ships being built today are too big to go through the enlarged Panama Canal, so it’s the smaller ships that will continue going through there.
We view the widening as an opportunity, because on the macro basis, you see shifts in manufacturing starting to occur. I was amazed after getting back from an extended trip to Latin America, looking at this first hand. All the Apple products now are being made in Brazil instead of China, because manufacturing in the Americas is as competitive—if not cheaper—than manufacturing of certain high-tech goods in Asia. We’re beginning to see moves on the manufacturing front that are going to drive a completely different supply chain in North American markets.
We also see the emergence of the economies in Latin America, driving volume both regionally and throughout the Americas. We should actually see an increased opportunity by movement from Latin America through the various ports and through the Panama Canal, up to the US markets. Our most conservative estimates say there will be a very small, single-digit impact initially to some of the cargo being diverted. But over the long haul, we think we’ll actually see increased volumes because of the changing macroeconomics of trade.
- Log in to post comments