TPR recently interviewed Steve Glenn, Founder and CEO of Plant Prefab, to discuss the company's groundbreaking approach to manufacturing prefab housing. With a newly established plant in Southern California and innovative collaborations, Cloud Apartments, Plant Prefab clearly is setting new benchmarks for the industry.
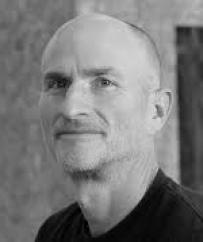
Steve Glenn
"We're not just building homes; we're redefining what prefab can be. Our new plant in Southern California allows us to tackle larger projects and bring unprecedented efficiency to affordable housing development."
TPR recently interviewed Steve Glenn, Founder and CEO of Plant Prefab, to discuss the company's groundbreaking approach to manufacturing prefab housing. With a newly established plant in Southern California and innovative collaborations, Cloud Apartments, Plant Prefab clearly is setting new benchmarks for the industry. Here, Glenn provides an in-depth look at how Plant Prefab's cutting-edge technology and smart design choices are driving down costs and accelerating construction timelines for affordable housing. From navigating the challenges of the 2008 real estate downturn to pioneering a hybrid prefab system that combines the best of both modules and panels, Glenn shares insights on the evolution of prefab housing internationally to shed light on its potential to address the domestic housing crisis. He also provides key insights on the strategic location and functionality of their production facility, their commitment to sustainability as a designated B Corporation, and the impact of permit reform and zoning on future projects.
Steve, with Plant Prefab’s recent agreement with Cloud Apartments to use module design and your company’s manufacturing expertise, please elaborate on your history with prefab housing, Plant Prefab’s mission, and your goals for your recently established manufacturing plant in Southern California.
Steve Glenn: Thank you for having me, and for being so generous in following our story over the years. As you know, we started 16 years ago when I founded a company called LivingHomes, focused on designing architecturally sustainable homes built through outsourced prefabrication. We began this journey in 2006, about a year before the worst real estate downturn since the Great Depression. If I had known that was coming, we probably wouldn't have started the company. The one and only advantage of that timing was that the factories we outsourced our work to weren't busy, so they took on our projects.
We ended up working with 10 different factories—half of which eventually closed. Working with world-class architects like Ray Kappe and Kieran Timberlake, we were often fighting gravity with the companies we partnered with. To be fair, they were primarily focused on building mobile homes and low-cost modular homes, which were quite different from the types of projects we were pursuing.
Post-downturn, we got really busy, as did the factories with whom we were working. It became clear that we needed a better solution. Initially, I didn’t think it made sense to have our factories, but I realized that if there were a new prefab company, one what wasn’t focused on standard, low-cost, non-sustainable homes — that’s what most of the existing supplier were going — but rather on customized work with any architect—really sustainable, high-quality homes—then that company could meet not only our needs but also the needs of hundreds of thousands of developers, affordable housing nonprofits, and others who wanted a better way to build their customized projects. That’s when we realized this was a huge opportunity, and we spun out Plant Prefab as a separate company eight years ago to pursue it. Plant eventually bought LivingHomes.
Here’s what we’re specifically focused on: In the U.S., prefab has traditionally been a product business. Companies like Cavco, Skyline, and Champion—the three biggest prefab companies, two of which are public, and one is owned by Warren Buffet—primarily produce mobile homes and low-cost modular homes. They don’t do much customization and don’t work with your architect. Since 2012, at the end of the downturn, we’ve seen unprecedented increases in land, labor, and material costs. A lot of labor left the market and hasn’t come back. Developers focused on infill communities, workforce housing, affordable housing, or second-home communities, our target market, face the most challenges because land and labor are most expensive, and labor is most scarce in these areas.
Adding to their challenge, at least for prefab, is the fact that infill developers need customization due the complexities of land and zoning regulations in cities, where there are dozens, if not hundreds, of different zoning variations, and lots come in many sizes. In addition to lot and zoning considerations, there are often great differences in design requirements and preferences.
Given the costs and time required to get projects completed and the increasing disparity between demand and supply at affordable and workforce housing levels, this multi-hundred billion construction market is in great need for innovation. But its not traditionally been the domain of prefab, which, again, has historically focused on specific products and has resisting any changes to those products.
This is Plant Prefab’s focus and we have a hybrid building system, a comprehensive engineering process, and the first facility in the US purpose built to manufacture both models and panels that allows us to best serve this market.
Until we opened the Tejon Ranch facility last year, we weren’t in a position to handle larger projects; we were focused on single-family and smaller multifamily projects. Now, with 270,000 square feet of space and automation, we can produce in much larger quantities and tackle bigger projects. What also sets us apart in the prefab industry is our unique and patented building system. Most companies you’ve heard of in prefab either do modules or panels, and each brings certain advantages and disadvantages. Modules are great because they allow you to build in an off-site controlled facility in parallel with site work, which helps compress the construction schedule. You can have all your skilled trades working simultaneously, which doesn’t typically happen on-site. This can reduce costs, particularly in California, where prevailing wage requirements apply in affordable housing. However, modules are expensive to ship and have a lot of redundant structures, making them particularly challenging for multifamily projects. Redundant walls and floors can force developers to rethink their total unit count or floor plan size to accommodate these structures. One last issue: modular projects must be designed and engineering for modular production. You cannot use plans that you may have designed and engineered for a site based process.
This is why some developers prefer panel systems, which are provide walls, floors, or roofs. Panels do not have redundant structure so they can typically accommodate most any design program and floor plan. Second, you do not have to design and engineer your plans specifically for panels, which is a real advantage, particularly for bidding. Third, panels ship flat, making them more efficient to transport and install. However, current panel systems, like Structural Insulated Panels (SIPs), still require a lot of on-site work, such as adding electrical, plumbing cladding, drywall, millwork, tiles, and appliances, which is time-consuming and expensive for particularly for the market we target.
The industry has traditionally forced you to choose between modules and panels. We offer both systems and work with our clients to solve their specific design requirements with the best solution possible based on their program, budget, schedule and site logistics.
Most of our projects employ both modules and panels. Modules are typically used for kitchens, bathrooms, stairs and utilities, the areas in a homes that are expensive to build, and panels often are a better solution for bedrooms, studies, hallways – spaces that are less complex. Some of our projects are all panels, particularly for projects that were design and engineered for site based construction and don’t have the time to revise their plans, and some projects are all modules. The point is that we don’t force clients to pick a building system and conform to it; we work with the client to find the best approach that works for them.
Steve, on June 10th, you announced a business relationship with Cloud Apartments and a housing project in Los Angeles—a six-story, 60-unit infill development. This project claims to be able to be produced at about half the cost and 30% faster than current affordable housing developments. Can you elaborate on the significance of the cost and time advantages of that housing project , especially considering the City of Los Angeles’ is prioritizating “affordable” housing development?
We actually have two affordable housing projects, and one of them is the one you mentioned. It's six stories and it's wood-frame construction. It turns out that if you use a two-hour fire separation between the floors, you can add an extra story in California, thanks to a state statute. We're also doing a 13-unit project in Santa Monica with the Community Corporation of Santa Monica, where Brooks + Scarpa is the architect.
The reason we’re able to do this more efficiently, both in terms of time and cost, is because of automation. We have about $15 million worth of automated equipment that allows us to create panels with minimal labor—super fast, and super efficient. Every module we create is made from these panels. We’re building in a controlled, all-weather environment at the Tejon Ranch factory that I mentioned earlier.
While site work is happening right now in Santa Monica, if you come to our factory, you’ll see the first tower—we're building two towers for this project. All the modules are being assembled now, and that’s how we compress the timeline. Our costs at the factory are much lower than the prevailing wage costs on-site in Santa Monica, as you can imagine.
Steve, elaborate on the significance of cost and time savings, given that “affordable housing” projects are now priced at “600,000 to $900,000 a door, which is not affordable. You’re suggesting, or at least in your announcement with Cloud Apartments, that Plant Prefab’s project will come in at in the $300,000—which is remarkable. Could you explain how that is achieved?
I think the average cost for an affordable housing unit in Los Angeles County is around $650,000, according to reports. For our Cloud Apartments project, we’ll do it at about half that cost. It’s a combination of smart design and super efficient production. Cloud Apartments is our partner on this project, and their model involves creating great flexible, reconfigurable, multifamily designs, with really smart choices of materials and construction details, tailored for specific lots, as well as fully negotiated supply chain agreements. We actually build a prototype for them for their market rates unit design, which we have in our factory. Anyone can come and see this.
We work very closely with Cloud Apartments, and they partner with developers—in this case, Genesis is the developer of the Koreatown project. The smart design leverages the super-efficient production capabilities we have, and we're building everything in parallel with the site work. Our labor rates are also less expensive than on-site labor rates, and that’s how we’re able to achieve these cost savings.
Steve, you also noted in your housing project’s announcement that speed and cost of delivery are advantages, which may explain why Plant Prefab has strategically located your facility in Tejon Ranch.
Could you elaborate on your decision to place the plant there and what it, in practice, means for reducing cost and delivery time?
We looked at California, Nevada, and Arizona, evaluating 13 potential sites. We ultimately narrowed it down to two: one in Reno and one in Tejon Ranch. Although we initially thought Reno might be the better choice, considering everything except for the regulatory environment, our Tejon Ranch site was the best choice. Although California has a less favorable regulatory environment versus Nevada, and Arvin has better labor rates, availability of the kind of labor we need, supply chain logistics, access to the population we serve, as well as utility rates.
We’re thrilled to be where we are, especially because most of us live in the area and can drive to Plant when we need to.
You also mentioned in the announcement that you have reusable, permit-ready designs for studio, one-bedroom, and two-bedroom units.
Can you explain what it means for these designs to be reusable and permit-ready?
So, big picture, one significant development is that prefab is evolving. Traditionally, prefab has been focused on low-cost, single-product solutions. However, a new generation of companies, like Cloud Apartments, is changing that. They’re among the smartest innovators in the multi-family prefab space right now.
Cloud Apartments has created reusable, permit-ready designs tailored for specific types of lots and zoning requirements. We invite anyone to come to our plant and tour their product, which includes furniture. Their model involves licensing these designs to developers, who then handle the land acquisition and financing. The supply chain is already negotiated with us, so developers only need to focus on the land and financing aspects. I think this is a smart model. Curtis Wong, their founding CEO, is leading this effort, and I believe we’ll see more products like this that target unique segments in real estate that have not previously been served by prefab solutions.
Could you speak to how the National Green Building Standard influences your design choices, particularly regarding energy, water, indoor air quality, and other aspects? How does this standard align with your mission focus?
We are a B Corp certified and we may be the only prefab Benefit Corporation. Being mission-driven, it’s part of our charter to reduce our ecological footprint, both for our operations and the buildings we produce.
Our facility itself is highly energy and water-efficient, as you can see from the solar panels in the background of the images I’ve shared. We’re committed to being as responsible as possible with respect to our energy use, water use, and the materials we use. Indoor air quality is also a key focus for us, as it's crucial for the health and well-being of our team members and the people who live in the homes we build
We work with various architects, so we don’t control every aspect of the design agenda since architects set the specifications. However, for the materials we order and the methods we use in our factory, we are very conscious of our environmental impact. For instance, we use recycled cellulose insulation, drywall made from 100% recycled material, LED downlights, and low-VOC paints and stains.
Regarding the economics of Plant Prefab, what’s your perspective, as a privately funded entity, on the size of the market for prefab housing? What, additionally, are the opportunities for investors in Plant Prefab?
In the broader context, prefab housing is much more advanced in other many other countries compared to the U.S. For example, in Japan, major home builders like Sekisui House, Daiwa House, and Toyota Home all employ prefab for their home projects. In Scandinavia, 70% of residential housing construction is via prefab. In fact, IKEA has a partnership with Skanska for multi-family housing projects.
Historically, these countries had higher costs for land, labor, and materials, which drove the adoption of prefab. As I said, since 2012, there has been an unprecedented increase in land, labor and material costs, creating even more motivation from developers to adopt methods that can make construction more time and cost efficient and dependable. Employed the right way, prefab can provide this – and can significantly help reduce the housing supply-demand gap in the U.S. As governments streamline the permitting process and potentially increase density, we expect to see more prefab housing, which could help improve affordability. Plant Prefab is positioned as a leading supplier in this sector, and long term, as we sell more panels, we’ll likely more like a building products supplier than a services company.
The market for prefab housing is growing, and while current interest rates have impacted real estate development, many believe the Fed may ease rates soon. Historically, real estate markets are cyclical, with up cycles following down cycles, and we anticipate doing even better when the market improves. If you look at home builders and building product companies, the latter are often valued higher. Companies like Lennar, D.R. Horton, and major building product firms have grown significantly through mergers and acquisitions. Similarly, as we prove our market growth, we will be considering M&A opportunities and potentially exploring public market options in the future if we continue to execute successfully.
Before concluding, Steve, when you spoke at VerdeXchange last May about the housing paradigm, you highlighted the significant need for permit & zoning reform to expedite more affordable housing projects. When you join us again at VX ( April 6-9 of 2025) do you think reform of both will still be a key theme and issue for your company?
Companies can drive significant innovation, but implementing change can take time. Permit and zoning reform will likely continue to be a key issue. However, there are promising opportunities for progress in this area. The California legislature has been proactive with initiatives like SB 9/10, among others, which have made strides in reforming permit processes and zoning. Execution at the local level can sometimes be challenging, and there are often delays. Nevertheless, as housing affordability becomes an increasingly pressing issue for the nation, there will be continued pressure to achieve breakthroughs that simplify and expedite these processes. I believe that by the time we meet again at the VX in April of next year, permit reform will still be a critical theme and an area of focus.
- Log in to post comments